La cartographie des flux de valeur est une technique permettant d’identifier et d’éliminer les déchets de processus. Il s’agit d’un type spécial d’organigramme qui utilise des symboles appelés « langage simplifié » pour décrire et améliorer l’inventaire et le flux d’informations. Cela nous aide à offrir aux clients la meilleure valeur grâce à un processus complet de création de valeur et à minimiser le gaspillage dans les aspects suivants :
- Conception (concept au client)
- Construire (de la commande à la livraison)
- Maintenir (en cours d’utilisation tout au long du cycle de vie jusqu’au service)
Qu’est-ce que la valeur pour les clients ?
La valeur est ce que le client achète, c’est-à-dire une capacité fournie à un client. Un produit ou un service fourni à un client doit être :
- De la plus haute qualité
- Au bon moment
- À un prix approprié tel que défini par le client
En réalité, les activités qui créent effectivement de la valeur pour les clients ne représentent qu’une petite partie de l’ensemble du processus de travail. C’est pourquoi les entreprises devraient se concentrer sur la réduction des activités inutiles autant que possible. Ce faisant, les entreprises peuvent identifier des opportunités significatives pour améliorer leur performance globale.
Qu’est-ce qu’un déchet ?
Daniel T. Jones (1995) identifie sept types de déchets communément acceptés. Ces termes sont mis à jour à partir de la nomenclature d’origine du système de production Toyota :
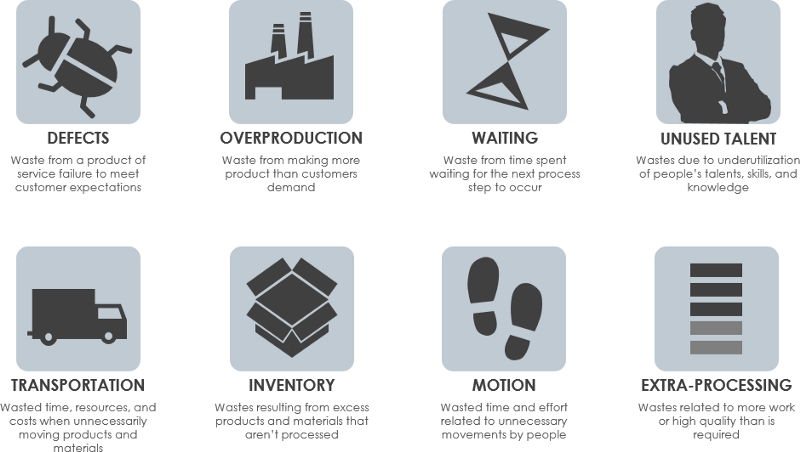
- Inventaire : acheter et stocker des matières premières, et stocker les travaux en cours pour attendre les processus futurs est un gaspillage.
- Attente : dans une série d’étapes de traitement d’un matériau, si l’une des étapes est lente, elle accumule alors le travail en cours, ce qui est un gaspillage.
- Défauts : Enfin, le type le plus important et le plus répandu est celui des défauts. Les défauts ne sont pas acceptables pour les clients. Pour éviter cela, un processus de contrôle de la qualité, le processus de reprise doit être établi, ce qui augmente les coûts. Par conséquent, les défauts sont une forme majeure de gaspillage.
- Surproduction : produire des articles qui dépassent la demande des clients.
- Mouvement : les mouvements inutiles des machines et les mouvements des opérateurs peuvent causer respectivement de l’usure et de la fatigue.
- Transport : tout mouvement inutile de travaux en cours ou de matières premières est une forme de déchet. Cela peut causer des dommages aux matériaux, et peut également augmenter le temps de cycle de production et est donc un gaspillage.
- Traitement excessif : fournir des fonctionnalités qui ne sont pas demandées par les clients et ajuster les niveaux au-delà de ceux prescrits par les clients, augmente le coût de fabrication, ce qui est un gaspillage.
Qu’est-ce qu’une analyse de flux de valeur ?
La cartographie des flux de valeur (VSM) est une technique fondamentale pour identifier les déchets et réduire les déchets de processus. Il s’agit d’un outil Lean essentiel pour une organisation qui souhaite planifier, mettre en œuvre et s’améliorer tout au long de son parcours Lean. Il aide les utilisateurs à créer un plan de mise en œuvre solide qui maximisera leurs ressources disponibles et contribuera à garantir que les matériaux et le temps sont utilisés efficacement. L’analyse de la chaîne de valeur est un puissant outil de planification pour optimiser le résultat de l’élimination du gaspillage.
VSM indique clairement le temps et les efforts consacrés aux activités sans valeur ajoutée, le coût de faire des affaires, et ouvre la voie à la réduction du gaspillage et à la rationalisation du processus. L’objectif de la cartographie des flux de valeur est de maximiser la valeur et de minimiser le gaspillage de plusieurs manières différentes, notamment :
- Faciliter une communication et une collaboration claires
- Encourager l’amélioration continue d’un processus
- Permettre le changement de culture au sein d’une organisation
- Création de visualisations des retards, des stocks excédentaires et des contraintes de production
Opération à valeur ajoutée vs sans valeur ajoutée
L’élimination des activités inutiles est cruciale pour le succès de votre entreprise. Ils peuvent réduire la rentabilité, augmenter les coûts des clients, diminuer la qualité et même la satisfaction des employés. Pour cette raison, vous devez identifier les activités sans valeur ajoutée et essayer d’améliorer le processus là où elles apparaissent ou finalement les éliminer.
Ne faites pas d’erreur. Toutes les activités inutiles ne peuvent pas être éliminées de votre processus de travail. Certains d’entre eux sont une nécessité.
Monden (1994) identifie trois types d’opérations :
- Opérations sans valeur ajoutée (NVA) : actions qui doivent être éliminées, telles que l’attente.
- Nécessaire mais sans valeur ajoutée (NNVA) : Actions inutiles mais nécessaires dans le cadre des procédures opérationnelles actuelles.
- Valeur Ajoutée (VA) : Conversion Ou Transformation De Matières Premières Via Le Travail Manuel.
En conclusion, les activités à valeur ajoutée doivent être davantage optimisées pour rechercher l’amélioration continue et la croissance d’une organisation, tandis que les activités sans valeur ajoutée doivent être éliminées, ou du moins minimisées autant que possible.
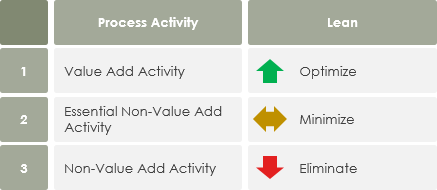
Exemple à valeur et sans valeur ajoutée — Déposer de l’argent dans un guichet automatique
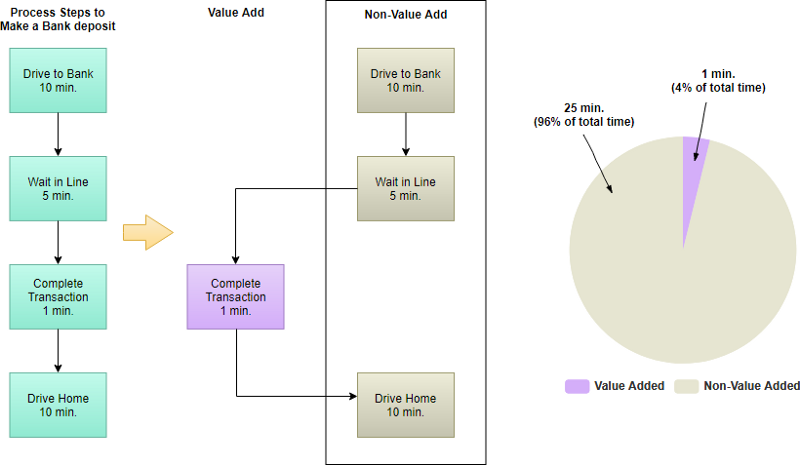
De la carte de flux de valeur de l’état actuel à la carte de flux de valeur de l’état futur
Comme mentionné précédemment, l’analyse de la chaîne de valeur est un outil de planification pour optimiser les résultats de l’élimination des déchets. Si vous créez uniquement une carte d’état actuelle, vous avez manqué l’objectif de VSM. La carte de l’état futur est une image du processus de transformation lean pour un flux de valeur spécifique. Avant de créer une carte d’état futur, vous devez déjà avoir créé une carte de flux de valeur d’état actuel.
Ainsi, l’analyse de flux de valeur cartographie visuellement le flux d’étapes, de retards et d’informations nécessaires pour fournir un produit ou un service ; c’est ce qu’on appelle une carte « État actuel ». Une carte de l’état futur identifie les améliorations à apporter au flux de valeur qui raccourciront le délai global.
Pour créer une carte d’état futur efficace, les éléments suivants doivent être pris en compte :
- Sélectionnez un produit pour la cartographie de la chaîne de valeur
- Créer une carte de flux de valeur actuelle
- Éliminer les déchets et créer une carte d’état futur plus efficace
- Créer un plan de mise en œuvre
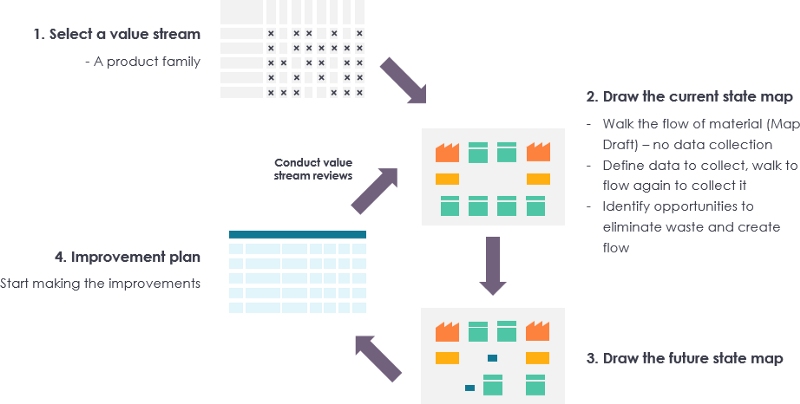
Enfin, vous devez créer un plan de mise en œuvre de la chaîne de valeur pour atteindre l’état futur. Vous êtes maintenant armé d’un plan pour une chaîne de valeur allégée que vous pouvez utiliser pour suivre/mesurer vos améliorations tout au long de l’année. Assurez-vous d’avoir un « responsable de la chaîne de valeur » ou un chef de projet qui dirige le plan jusqu’à son achèvement.
Exemple d’analyse de la chaîne de valeur — Contrôle de la production
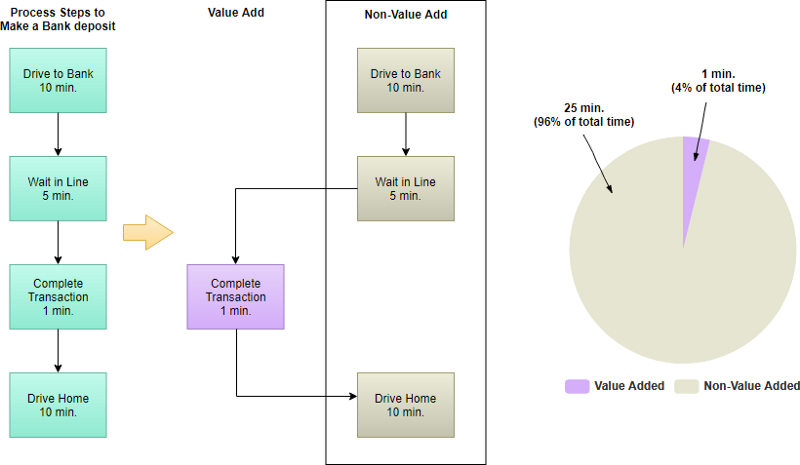
Cartographie de la chaîne de valeur – Autre exemple
Les cartes de flux de valeur peuvent être créées en suivant les étapes ci-dessous :
- La première étape de la cartographie des flux de valeur consiste à dessiner les BOÎTES DE PROCESSUS pour les différentes étapes du processus, en partant du côté fournisseur jusqu’au côté client dans la zone des flux d’informations.
- La deuxième étape dessine les différents types de boîtes de processus pour différents types d’étapes de production dans la section de flux d’informations appelée Flux de matières.
- La troisième étape de la cartographie de la chaîne de valeur est constituée de DATABOXES juste sous chacune des étapes de processus (ou de production), dans laquelle les données sont capturées pour chacune des étapes de processus dessinées dans la carte. Les informations qui pourraient être intéressantes pour la conception VSM peuvent être mises ici.
- La quatrième étape consiste à dessiner les MÉTHODES DE CONNEXION entre les boîtes de processus.
- La cinquième étape décrit la liaison des CLIENTS ET FOURNISSEURS au processus.
- La cinquième étape est le LEAD TIME LADDER au bas du VSM, qui montre différents aspects du temps dans le flux de valeur.
L’exemple ci-dessous montre à quoi pourrait ressembler une carte de flux de valeur typique :
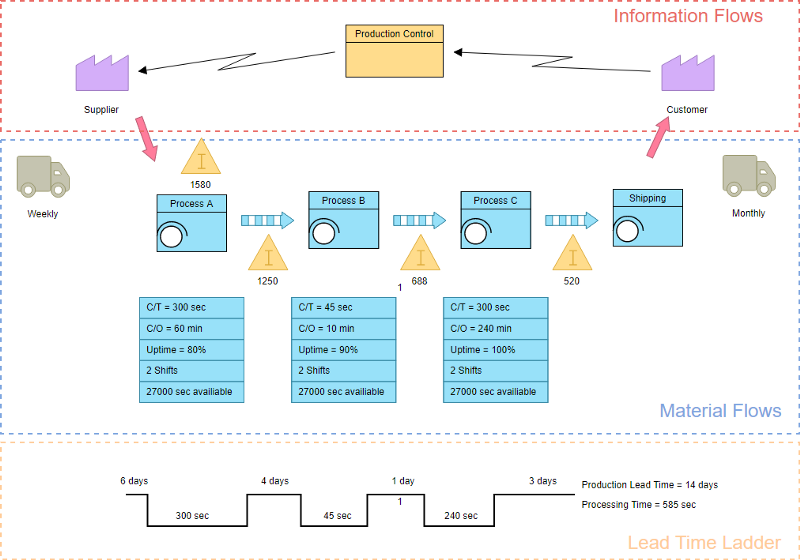
Élaboration d’un plan de mise en œuvre continue
VSM aide les utilisateurs à créer un plan de mise en œuvre solide qui maximisera leurs ressources disponibles et contribuera à garantir que les matériaux et le temps sont utilisés efficacement. Sur la base des informations fournies par la future carte, nous pouvons maintenant élaborer un plan de mise en œuvre des actions nécessaires pour passer de l’état actuel à l’état futur. Voici un modèle générique fourni comme suit :
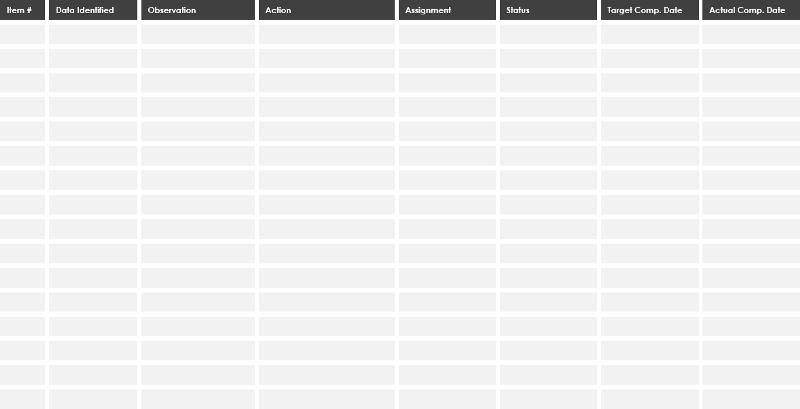
Composants de la cartographie des flux de valeur
Symboles / Description

Client/Fournisseur : représente le fournisseur lorsqu’il est en haut à gauche, le client lorsqu’il est en haut à droite, le point de terminaison habituel pour le matériel

Flux de processus dédié : un processus, une opération, une machine ou un département, à travers lequel le matériau circule. Il représente un département avec un flux fixe interne continu.

Processus partagé : un processus, une opération, un service ou 11 Processus partagé : un processus, une opération ou un service que d’autres familles de flux de valeur partagent.

Boîte de données : elle contient des informations/données importantes nécessaires à l’analyse et à l’observation du système.

Cellule de travail : indique que plusieurs processus sont intégrés dans une cellule de travail de fabrication.

Inventaire : affiche l’inventaire entre deux processus

Expéditions : représente le mouvement des matières premières des fournisseurs vers le(s) quai(s) de réception de l’usine. Ou, le mouvement des produits finis du ou des quais d’expédition de l’usine vers les clients

Pousser la flèche : représente le « poussée » du matériau d’un processus au processus suivant.

Supermarché : un « supermarché » d’inventaire.

Material Pull : les supermarchés se connectent aux processus en aval avec ce « Pull » qui indique le retrait physique.

FIFO Lane : Inventaire First-In-First-Out. Utilisez-le lorsque les processus sont connectés à un système FIFO qui limite l’entrée.

Stock de sécurité : représente une « couverture » d’inventaire (ou stock de sécurité) contre des problèmes tels que les temps d’arrêt, pour protéger le système contre les fluctuations soudaines des commandes des clients ou les défaillances du système.

Expédition externe : expéditions des fournisseurs ou aux clients utilisant le transport externe

Contrôle de la production : cette case représente un service central de planification ou de contrôle de la production, une personne ou une opération.

Infos manuelles : une flèche fine et droite indique le flux général d’informations à partir de mémos, de rapports ou de conversations. La fréquence et d’autres notes peuvent être pertinentes.

Information électronique : cette flèche oscillante représente les flux électroniques 14 tels que l’échange de données informatisé (EDI), l’Internet, les Intranets, les LAN (réseau local), les WAN (réseau étendu). Vous pouvez indiquer la fréquence des échanges d’informations/données, le type de média utilisé, ex. fax, téléphone, etc. et le type de données échangées.

Production Kanban : il déclenche la production d’un nombre prédéfini de pièces. Il signale à un processus d’approvisionnement de fournir des pièces à un processus en aval.

Kanban retiré : il représente une carte ou un dispositif qui ordonne à un manutentionnaire de transférer des pièces d’un supermarché vers le processus de réception. Le manutentionnaire (ou l’opérateur) se rend au supermarché et retire les articles nécessaires.

Signal Kanban : utilisé chaque fois que les niveaux de stock disponibles dans le supermarché entre deux processus chutent à un seuil de déclenchement ou minimum. Il est également appelé Kanban « un par lot ».

Kanban Post : un emplacement où résident les signaux Kanban pour le ramassage. Souvent utilisé avec les systèmes à deux cartes pour échanger le Kanban de retrait et de production.

Sequence Pull : représente un système pull qui donne l’instruction 15 aux processus de sous-assemblage pour produire un type et une quantité de produit prédéterminés, généralement une unité, sans passer par un supermarché.

Load Leveling : un outil de batch Kanban pour niveler le volume de production et mélanger sur un certain temps.

Go See Production : la collecte d’informations par des moyens visuels

Information verbale : représente le flux d’informations verbales ou personnelles

Kaizen : utilisé pour mettre en évidence les besoins d’amélioration et planifier des ateliers Kaizen sur des processus spécifiques qui sont essentiels à la réalisation de la carte de l’état futur de la chaîne de valeur.

Opérateur : représente un opérateur. Il indique le nombre d’opérateurs nécessaires pour traiter la famille VSM sur un poste de travail particulier.

Autres informations : autres informations utiles ou potentiellement utiles.

Timeline : affiche les temps à valeur ajoutée (Cycle Times) et les temps sans valeur ajoutée (wait). Utilisez ceci pour calculer le délai d’approvisionnement et le temps de cycle total.
Terminologie de la cartographie des flux de valeur
- C/T (Temps de cycle) : Temps de cycle du processeur = Temps nécessaire pour terminer une tâche.
- P /T ou C/O (Temps de changement) : Le temps sans valeur ajoutée requis pour convertir une ligne d’un produit à un autre Temps de changement ou temps de configuration pour commencer une nouvelle tâche.
- VA (Value Added Task ) : Temps à valeur ajoutée ou temps nécessaire pour effectuer une tâche requise.
- NVA (None Value Added Task) : Temps sans valeur ajoutée = PT — TVA.
- L/T (Lead Time) : Délai d’exécution ou temps total entre le démarrage d’une tâche dans un poste de travail et son départ du poste de travail.
- FTT (First Time Through) : qualité du premier coup ou rendement de qualité du premier coup.
- T/T (Takt Time) : Le temps de production unitaire moyen nécessaire pour répondre à la demande du client.
- Capacité : Une métrique qui indique combien de pièces par jour votre processus le plus lent peut traiter.
Outil de cartographie de la chaîne de valeur
Vous recherchez un logiciel VSM ? Le logiciel de cartographie de la chaîne de valeur Visual Paradigm peut facilement et rapidement créer une cartographie professionnelle de la chaîne de valeur. L’outil de mappage de flux de valeur est fourni avec un riche ensemble de symboles de mappage de flux de valeur. Avec un éditeur VSM par glisser-déposer et un ensemble de fonctionnalités puissantes, vous pouvez facilement créer des cartes de flux de valeur professionnelles.
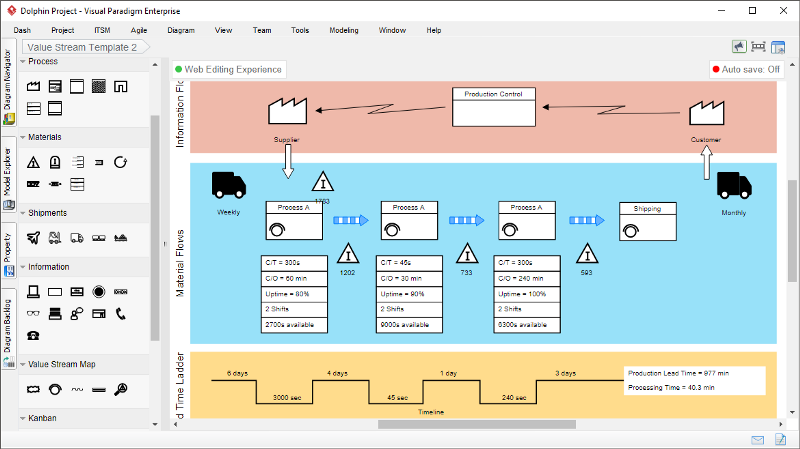
Apprendre par des exemples — Modèles de cartographie de flux de valeur
Vous pouvez essayer de les modifier en ligne en cliquant sur le lien d’exemple ci-dessous :
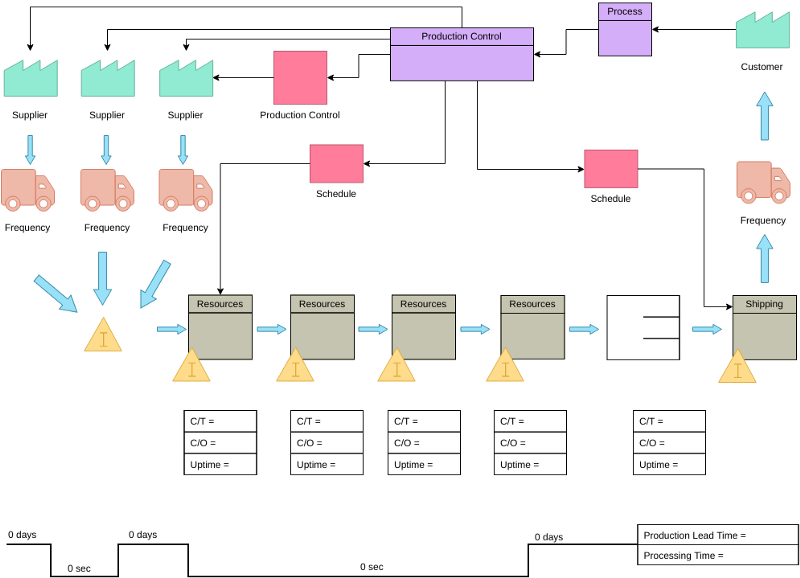
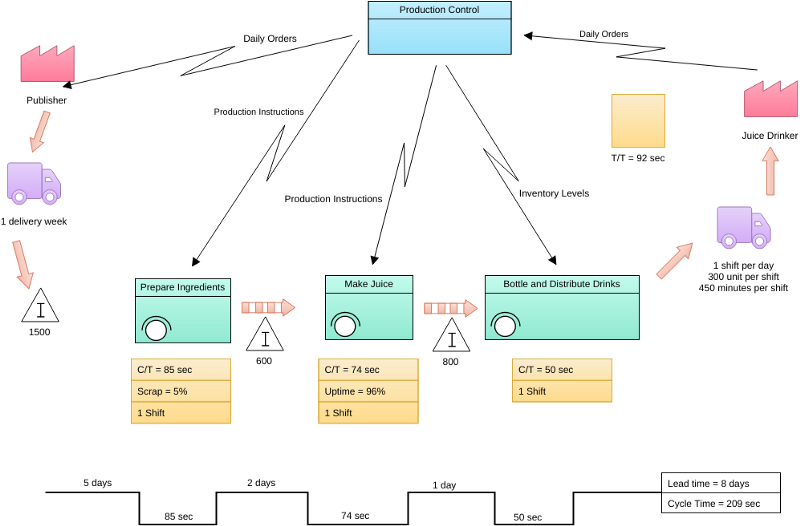
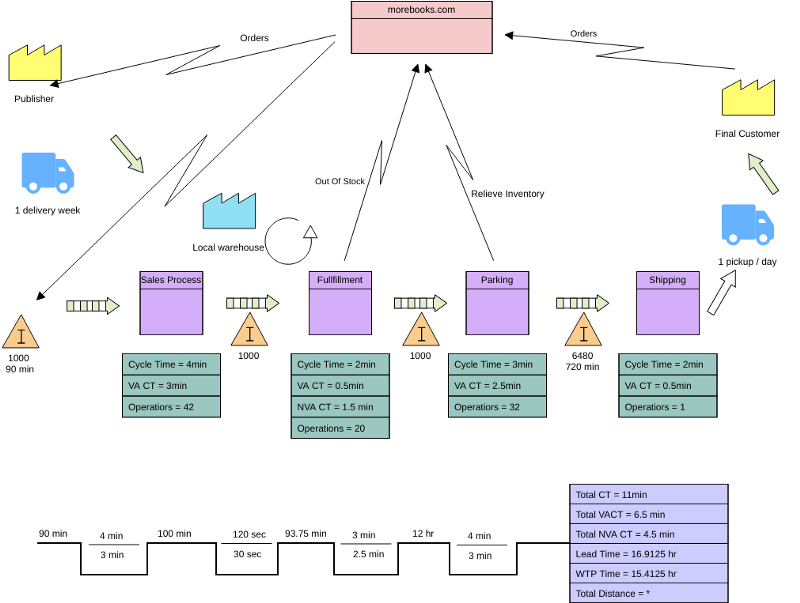
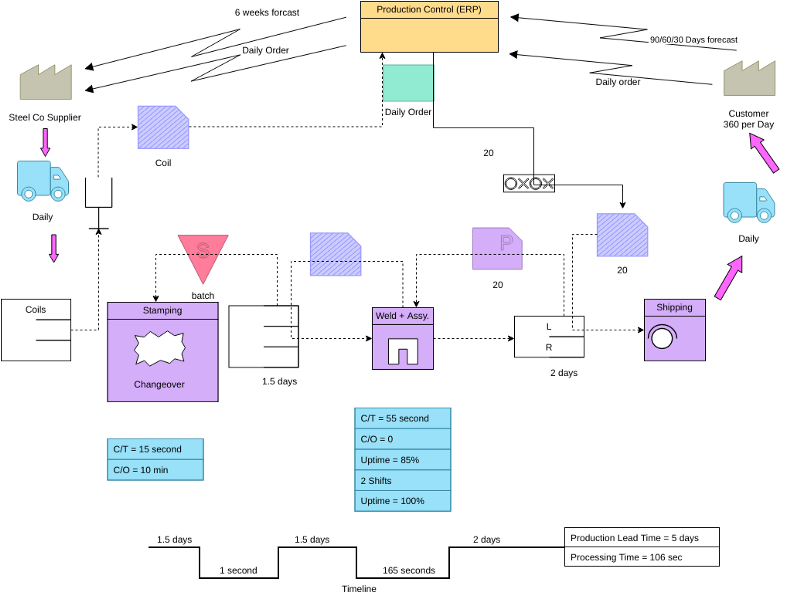
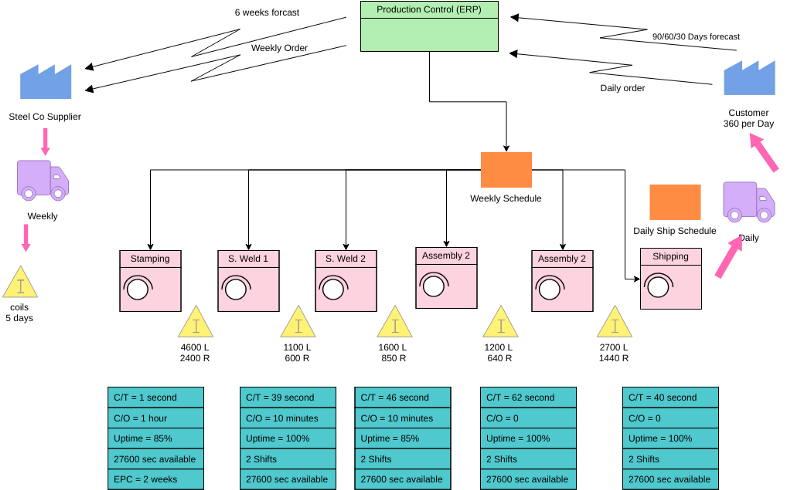
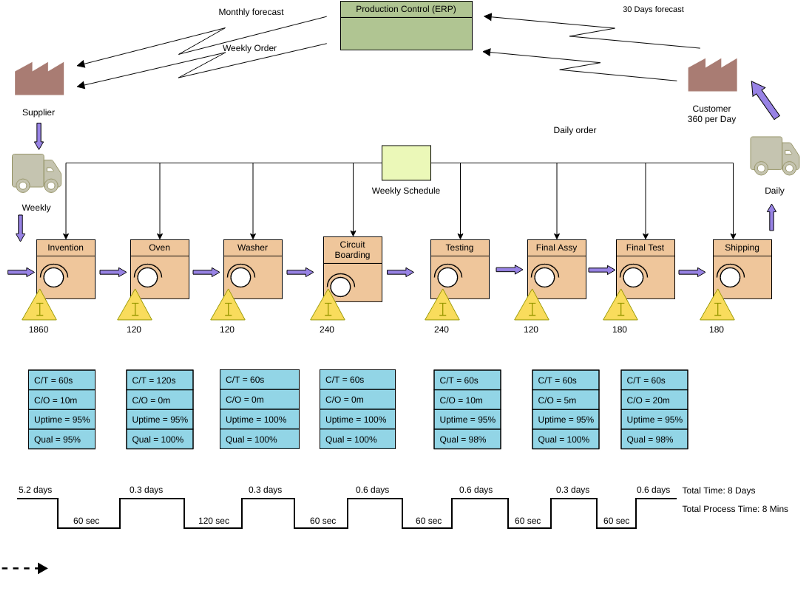
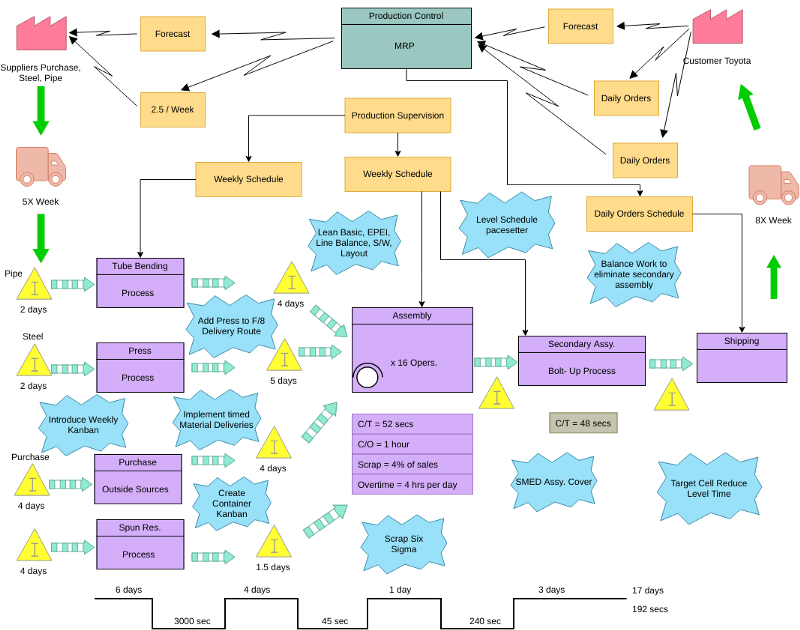
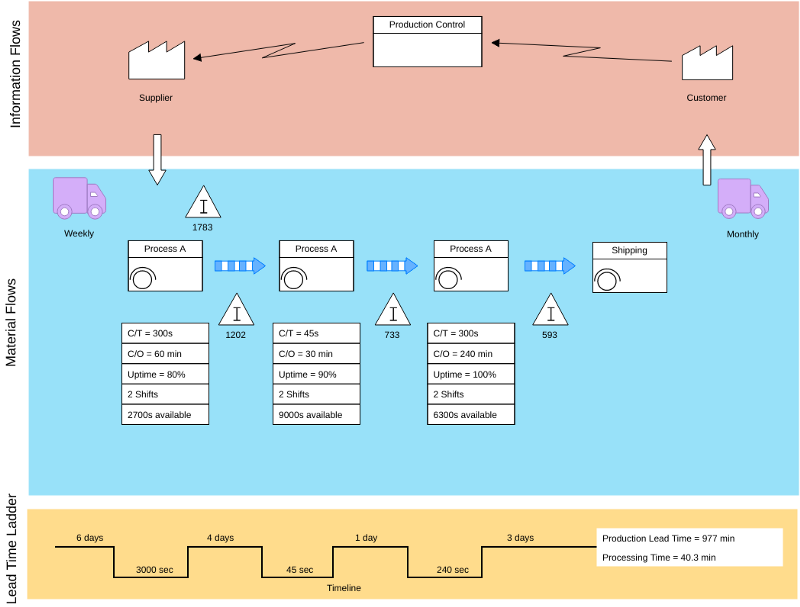
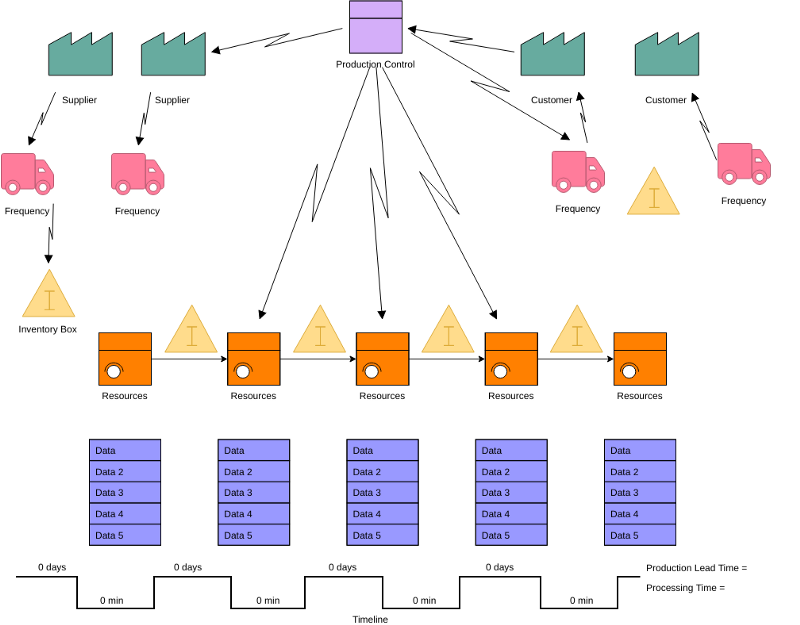
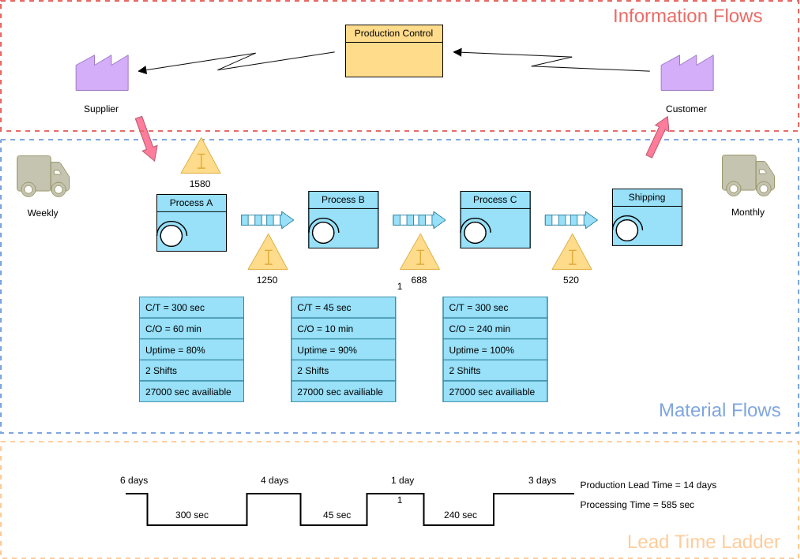
Cette publication est également disponible en Deutsch, English, Español, فارسی, Bahasa Indonesia, 日本語, Polski, Portuguese, Ру́сский, Việt Nam, 简体中文 : liste des langues séparées par une virgule, 繁體中文 : dernière langue.