O mapeamento do fluxo de valor é uma técnica para identificar e eliminar o desperdício do processo. É um tipo especial de fluxograma que usa símbolos chamados “linguagem enxuta” para descrever e melhorar o fluxo de estoque e informações. Ele nos ajuda a oferecer aos clientes o melhor valor por meio de um processo completo de criação de valor e minimizar o desperdício nos seguintes aspectos:
- Design (conceito para o cliente)
- Construir (pedido para entrega)
- Sustentar (em uso ao longo do ciclo de vida até o serviço)
O que é Valor para os Clientes?
Valor é o que o cliente está comprando, que é uma capacidade fornecida a um cliente. Um produto ou serviço fornecido a um cliente deve ser:
- Da mais alta qualidade
- No tempo certo
- A um preço apropriado conforme definido pelo cliente
Na realidade, as atividades que realmente criam valor para os clientes são apenas uma pequena parte de todo o processo de trabalho. É por isso que as empresas devem se concentrar em reduzir ao máximo as atividades que geram desperdício. Ao fazer isso, as empresas podem identificar oportunidades significativas para melhorar seu desempenho geral.
O que é Resíduos?
Daniel T. Jones (1995) identifica sete tipos de resíduos comumente aceitos. Estes termos são atualizados a partir da nomenclatura original do sistema de produção Toyota:
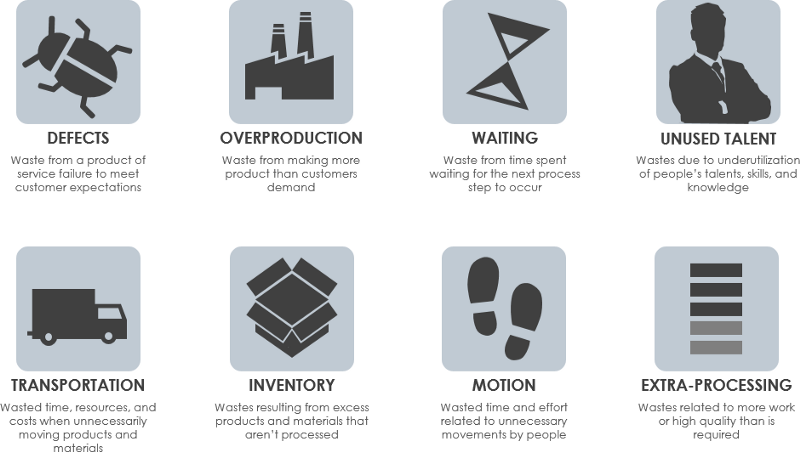
- Estoque: Comprar e armazenar matérias-primas e estocar o trabalho em andamento para aguardar os processos futuros é um desperdício.
- Espera: em uma série de etapas para processar um material, se uma das etapas for lenta, acumulará trabalho em andamento que é um desperdício.
- Defeitos: Finalmente, o tipo mais importante e prevalente são os defeitos. Defeitos não são aceitáveis para os clientes. Para evitar isso, um processo de verificação de qualidade, o processo de retrabalho deve ser estabelecido, o que aumenta o custo. Portanto, os defeitos são uma forma importante de desperdício.
- Superprodução: Produzindo itens que estão em excesso de demanda do cliente.
- Movimento: Movimento desnecessário de máquinas e movimentos de operadores podem causar desgaste e fadiga, respectivamente.
- Transporte: Qualquer Movimentação Desnecessária de Obras em Andamento ou Matérias-Primas é uma forma de desperdício. Isso pode causar danos aos materiais, e também pode aumentar o tempo de ciclo de produção e, portanto, é um desperdício.
- Processamento excessivo: fornecer recursos que não são exigidos pelos clientes e ajustar os níveis mais do que os prescritos pelos clientes aumenta o custo de fabricação, o que é um desperdício.
O que é uma análise de fluxo de valor?
O Mapeamento do Fluxo de Valor (VSM) é uma técnica fundamental para identificar desperdícios e reduzir o desperdício do processo. É uma ferramenta lean essencial para uma organização que deseja planejar, implementar e melhorar durante sua jornada lean. Ele ajuda os usuários a criar um plano de implementação sólido que maximizará seus recursos disponíveis e ajudará a garantir que os materiais e o tempo sejam usados com eficiência. A Análise de Fluxo de Valor é uma poderosa ferramenta de planejamento para otimizar o resultado da eliminação de desperdícios.
O VSM deixa claro o tempo e o esforço gastos em atividades que não agregam valor, o custo de fazer negócios e prepara o cenário para reduzir o desperdício e simplificar o processo. O objetivo do mapeamento do fluxo de valor é maximizar o valor e minimizar o desperdício de várias maneiras, incluindo:
- Facilitando a comunicação e a colaboração claras
- Incentivando a Melhoria Contínua de um Processo
- Permitindo a mudança de cultura dentro de uma organização
- Criando visualizações de atrasos, excesso de estoque e restrições de produção
Operação de Valor Agregado vs Sem Valor Agregado
Eliminar atividades desnecessárias é crucial para o sucesso da sua empresa. Eles podem diminuir a lucratividade, aumentar os custos do cliente, diminuir a qualidade e até mesmo a satisfação dos funcionários. Por esse motivo, você precisa identificar as atividades que não agregam valor e tentar melhorar o processo onde elas aparecem ou, finalmente, eliminá-las.
Não cometa um erro. Nem todas as atividades desnecessárias podem ser eliminadas do seu processo de trabalho. Alguns deles são uma necessidade.
Monden (1994) identifica três tipos de operações:
- Operações sem valor agregado (NVA): Ações que devem ser eliminadas, como espera.
- Necessário, mas que não agrega valor (NNVA): Ações que são desnecessárias, mas que são desnecessárias sob os procedimentos operacionais atuais.
- Agregação de Valor (VA): Conversão ou Processamento de Matérias-Primas via Mão de Obra.
Em conclusão, as atividades de valor agregado devem ser otimizadas ainda mais para buscar a melhoria contínua e o crescimento de uma organização, enquanto as atividades sem valor agregado devem ser eliminadas, ou pelo menos minimizadas ao máximo.
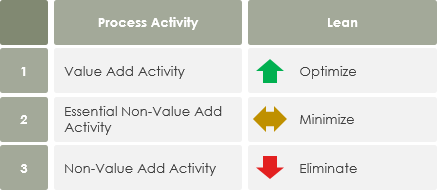
Exemplo de valor e sem valor agregado – Depositar dinheiro em caixa eletrônico
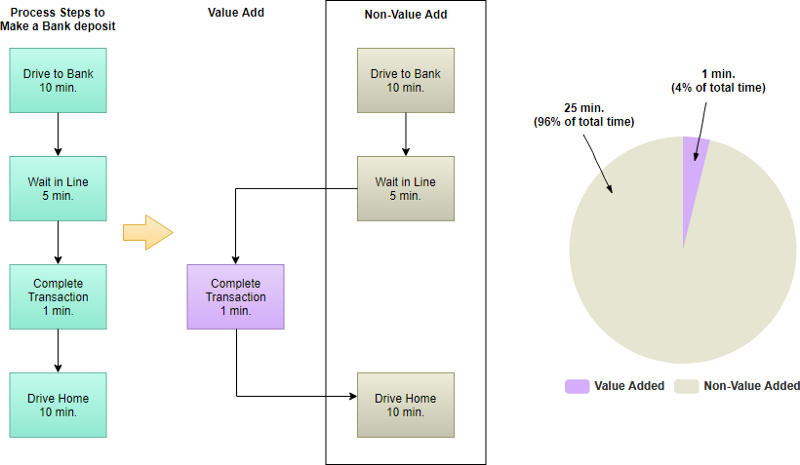
Do mapa do fluxo de valor do estado atual para o mapa do fluxo de valor do estado futuro
Como mencionado anteriormente, a Análise do Fluxo de Valor é uma ferramenta de planejamento para otimizar os resultados da eliminação de desperdícios. Se você criar apenas um mapa de estado atual, você perdeu a finalidade do VSM. O mapa do estado futuro é uma imagem do processo de transformação lean para um fluxo de valor específico. Antes de criar um mapa de estado futuro, você já deve ter criado um mapa de fluxo de valor do estado atual.
Assim, a Análise do Fluxo de Valor mapeia visualmente o fluxo de etapas, atrasos e informações necessárias para entregar um produto ou serviço; isso é chamado de Mapa de “Estado Atual”. Um mapa de estado futuro identifica melhorias a serem feitas no fluxo de valor que reduzirão o lead time geral.
Para criar um mapa de estado futuro eficaz, o seguinte deve ser considerado:
- Selecione um produto para mapeamento de fluxo de valor
- Criar um mapa de fluxo de valor atual
- Elimine o desperdício e crie um mapa do estado futuro mais eficiente
- Criar um plano de implementação
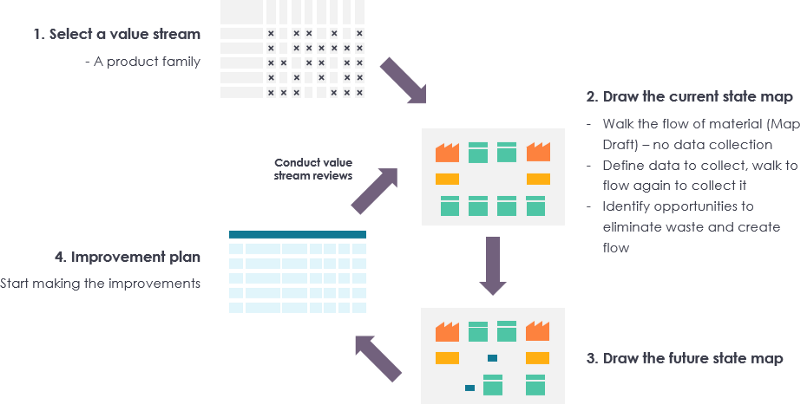
Finalmente, você deve criar um plano de implementação do fluxo de valor para atingir o estado futuro. Agora você está armado com um plano para um fluxo de valor enxuto que pode ser usado para acompanhar/medir suas melhorias ao longo do ano. Certifique-se de que você tenha um “gerente de fluxo de valor” ou gerente de projeto conduzindo o plano até a conclusão.
Exemplo de Análise de Fluxo de Valor – Controle de Produção
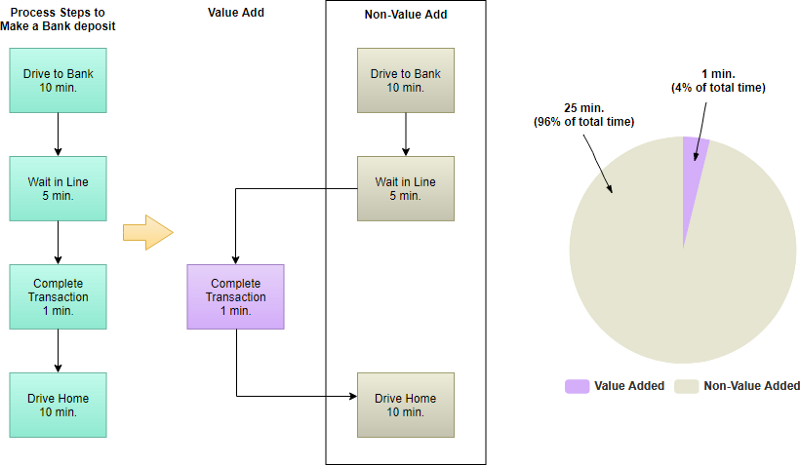
Mapeamento do fluxo de valor – outro exemplo
Os mapas de fluxo de valor podem ser criados seguindo as etapas abaixo:
- O primeiro passo no mapeamento do fluxo de valor é desenhar as CAIXAS DE PROCESSO para as diferentes etapas do processo, começando do lado do fornecedor até o lado do cliente na área de fluxos de informação.
- A segunda etapa desenha os diferentes tipos de caixas de processo para diferentes tipos de etapas de produção na seção de fluxo de informações chamada fluxos de materiais.
- A terceira etapa no mapeamento do fluxo de valor é DATABOXES logo abaixo de cada um dos processos (ou etapas de produção), em que os dados são capturados de cada uma das etapas do processo desenhadas no mapa. Informações que podem ser interessantes para o design do VSM podem ser colocadas aqui.
- O quarto passo é desenhar os MÉTODOS DE CONEXÃO entre as caixas de processo.
- A quinta etapa descreve a vinculação de CLIENTES E FORNECEDORES ao processo.
- A etapa cinco é a LEAD TIME LADDER na parte inferior do VSM, que mostra diferentes aspectos do tempo no fluxo de valor.
O exemplo abaixo mostra como pode ser um mapa de fluxo de valor típico:
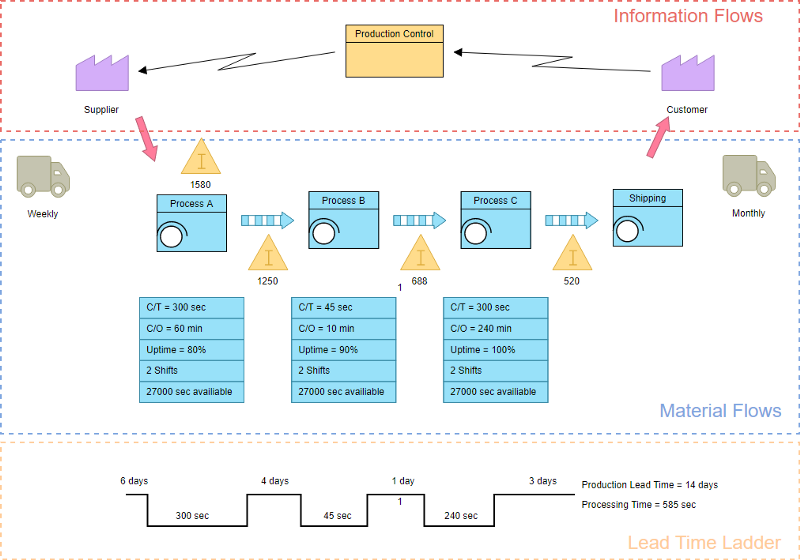
Desenvolvendo um Plano de Implementação Contínua
O VSM ajuda os usuários a criar um plano de implementação sólido que maximizará seus recursos disponíveis e ajudará a garantir que os materiais e o tempo sejam usados com eficiência. Com base nas informações fornecidas pelo mapa futuro, podemos agora desenvolver um plano de implementação das ações necessárias para ir do estado atual ao estado futuro. Aqui está um modelo genérico fornecido da seguinte forma:
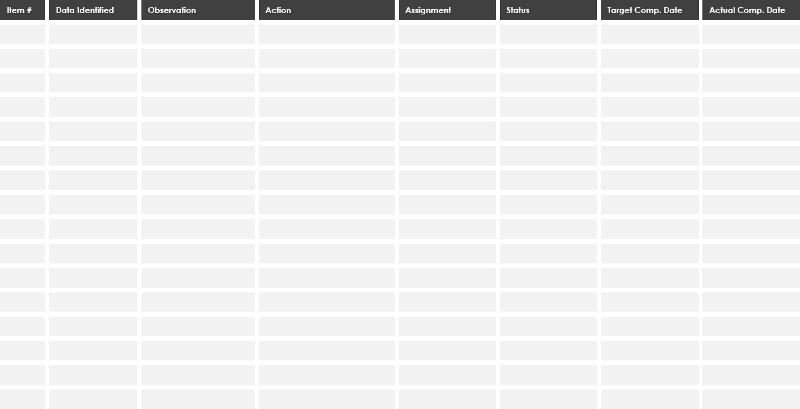
Componentes do Mapeamento do Fluxo de Valor
Símbolos / Descrição

Cliente/Fornecedor : representa o Fornecedor quando no canto superior esquerdo, o cliente no canto superior direito, o ponto final usual para material

Fluxo de Processo Dedicado : um processo, operação, máquina ou departamento, através do qual o material flui. Representa um departamento com um fluxo fixo interno contínuo.

Processo Compartilhado : um processo, operação, departamento ou 11 Processo Compartilhado: um processo, operação ou departamento que outras famílias de fluxo de valor compartilham.

Data Box : contém informações/dados significativos necessários para analisar e observar o sistema.

Célula de Trabalho : indica que vários processos estão integrados em uma Célula de Trabalho de Manufatura.

Inventário : mostra o inventário entre dois processos

Embarques : representa a movimentação de matérias-primas dos fornecedores para as docas de recebimento da fábrica. Ou, a movimentação de produtos acabados das docas de embarque da fábrica para os clientes

Seta de Empurrão : representa o “empurrão” de material de um processo para o próximo processo.

Supermercado : um “supermercado” de estoque.

Material Pull : os supermercados se conectam aos processos downstream com este “Pull” que indica a remoção física.

FIFO Lane : Inventário First-In-First-Out. Use-o quando os processos estiverem conectados a um sistema FIFO que limita a entrada.

Estoque de Segurança : representa um “hedge” de estoque (ou estoque de segurança) contra problemas como paralisações, para proteger o sistema contra flutuações repentinas nos pedidos dos clientes ou falhas no sistema.

Remessa Externa : remessas de fornecedores ou para clientes usando transporte externo

Controle de Produção : esta caixa representa uma programação central de produção ou departamento de controle, pessoa ou operação.

Informações manuais : uma seta reta e fina mostra o fluxo geral de informações de memorandos, relatórios ou conversas. A frequência e outras notas podem ser relevantes.

Informações Eletrônicas : esta seta ondulada representa o fluxo eletrônico 14, como intercâmbio eletrônico de dados (EDI), Internet, Intranets, LANs (rede local), WANs (rede de área ampla). Você pode indicar a frequência do intercâmbio de informações/dados, o tipo de mídia utilizada ex. fax, telefone, etc. e o tipo de dados trocados.

Kanban de Produção : aciona a produção de um número pré-definido de peças. Ele sinaliza um processo de fornecimento para fornecer peças para um processo a jusante.

Kanban retirado : representa um cartão ou dispositivo que instrui um manipulador de materiais a transferir peças de um supermercado para o processo de recebimento. O manipulador de materiais (ou operador) vai ao supermercado e retira os itens necessários.

Sinal Kanban : usado sempre que os níveis de estoque disponível no supermercado entre dois processos caem para um ponto de gatilho ou mínimo. Também é conhecido como Kanban “um por lote”.

Posto Kanban : um local onde os sinais Kanban residem para retirada. Frequentemente usado com sistemas de dois cartões para troca de Kanban de retirada e produção.

Sequência Pull : representa um sistema puxado que dá a instrução 15 aos processos de submontagem para produzir um tipo e quantidade predeterminada de produto, normalmente uma unidade, sem usar um supermercado.

Load Leveling : uma ferramenta para batch Kanban para nivelar o volume de produção e misturar ao longo do tempo.

Go See Production : a recolha de informação através de meios visuais

Informação Verbal : representa o fluxo de informação verbal ou pessoal

Kaizen : usado para destacar necessidades de melhoria e planejar workshops de kaizen em processos específicos que são críticos para alcançar o Mapa do Estado Futuro do fluxo de valor.

Operador : representa um operador. Ele mostra o número de operadores necessários para processar a família VSM em uma determinada estação de trabalho.

Outras informações : outras informações úteis ou potencialmente úteis.

Linha do tempo : mostra os tempos de valor agregado (tempos de ciclo) e os tempos sem valor agregado (espera). Use isso para calcular o tempo de espera e o tempo total do ciclo.
Terminologia do mapa de fluxo de valor
- C/T (Tempo de Ciclo) : Tempo de Ciclo do Processador = Tempo para Concluir uma Tarefa.
- P /T ou C/O (tempo de troca) : o tempo sem valor agregado necessário para converter uma linha de um produto para outro tempo de troca ou tempo de configuração para iniciar uma nova tarefa.
- VA (Tarefa de Valor Agregado ): Tempo de Valor Agregado ou Tempo Necessário para Concluir uma Tarefa Necessária.
- NVA (Nenhuma Tarefa de Valor Agregado): Tempo sem Valor Agregado = PT — IVA.
- L/T (Lead Time) : Lead Time, ou o tempo total de quando uma tarefa é iniciada dentro de um centro de trabalho até sair do centro de trabalho.
- FTT (First Time Through) : Qualidade na Primeira Vez ou Rendimento da Primeira Vez.
- T/T (Takt Time) : O Tempo Médio de Produção Unitário Necessário Para Atender à Demanda do Cliente.
- Capacidade : Uma métrica que indica quantas peças por dia seu processo mais lento pode processar.
Ferramenta de mapeamento de fluxo de valor
Procurando por software VSM? O software de mapeamento de fluxo de valor Visual Paradigm pode criar fácil e rapidamente mapeamento de fluxo de valor profissional. A ferramenta de mapeamento de fluxo de valor vem com um rico conjunto de símbolos de mapeamento de fluxo de valor. Com um editor VSM de arrastar e soltar e um poderoso conjunto de recursos, você pode criar facilmente mapas profissionais de fluxo de valor.
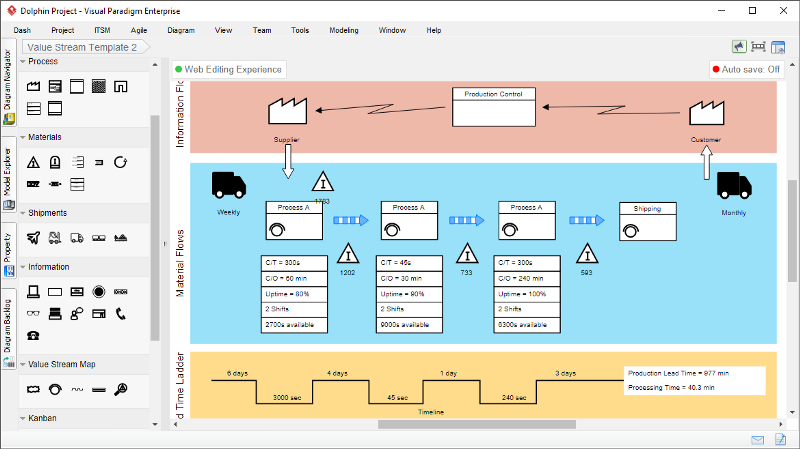
Aprenda por exemplos — modelos de mapeamento de fluxo de valor
Você pode tentar editá-los online clicando no link de exemplo abaixo:
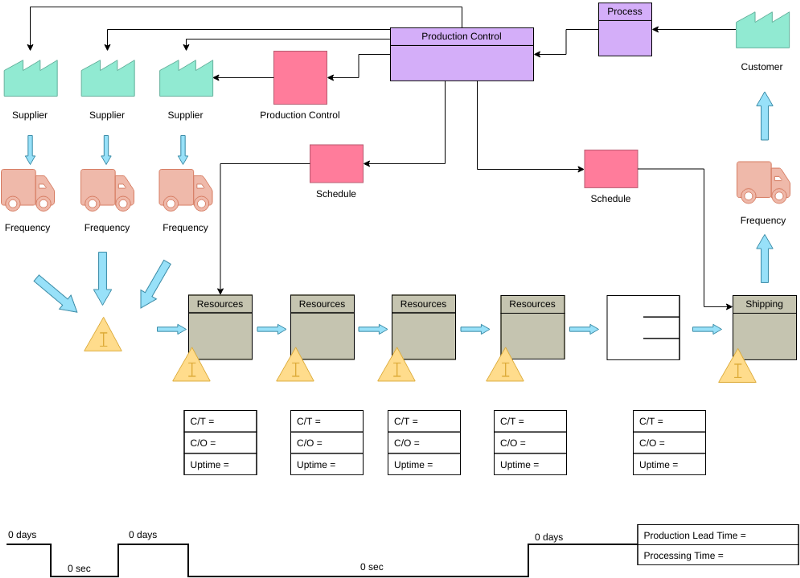
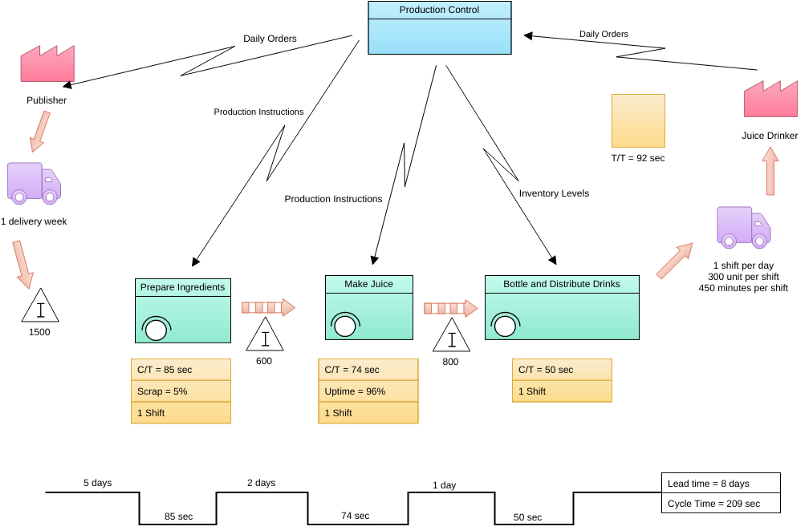
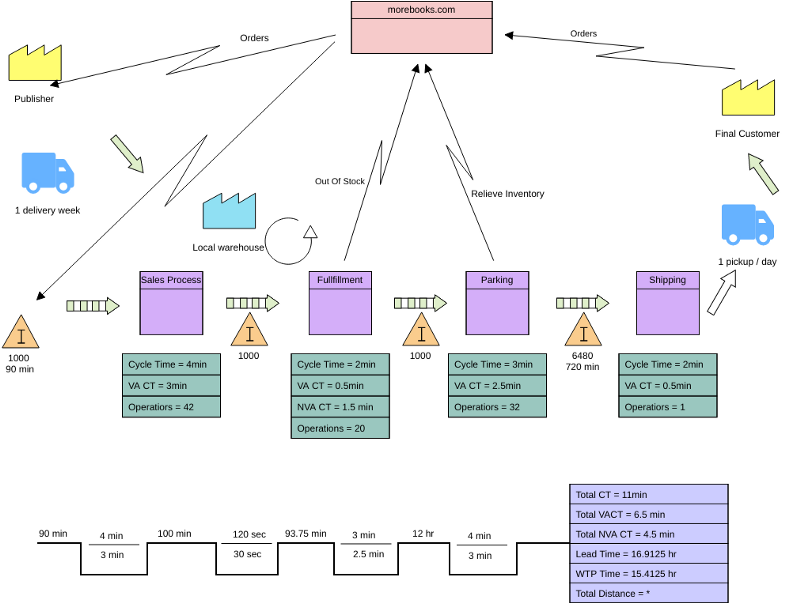
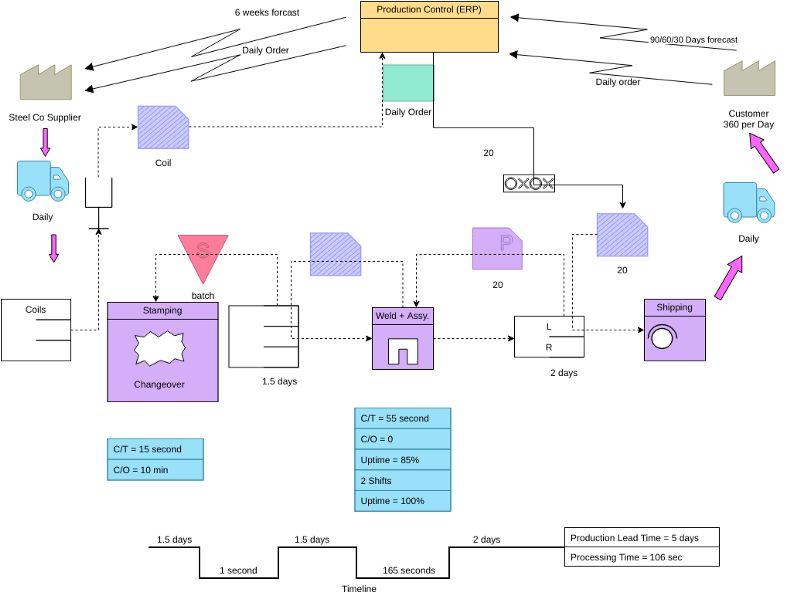
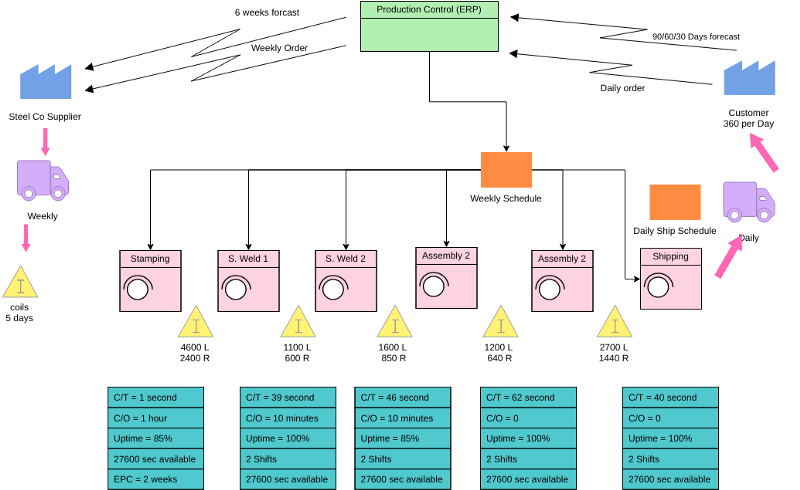
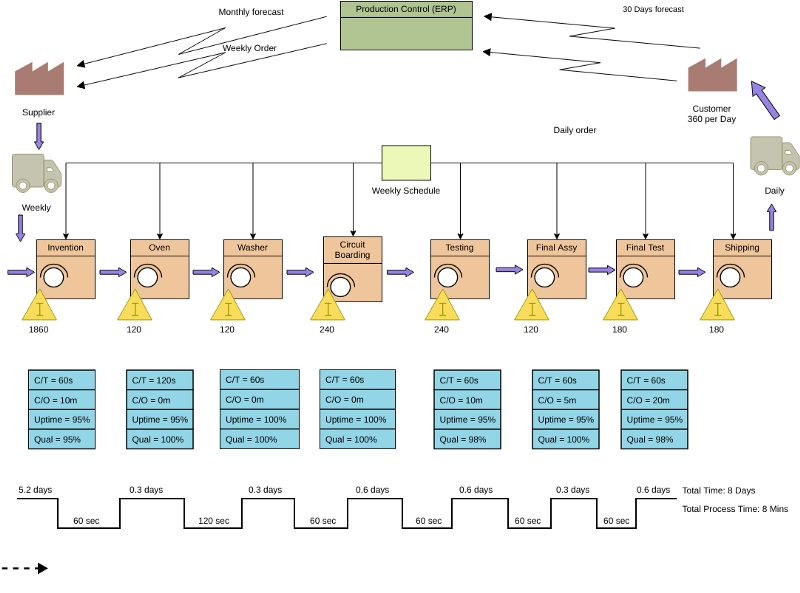
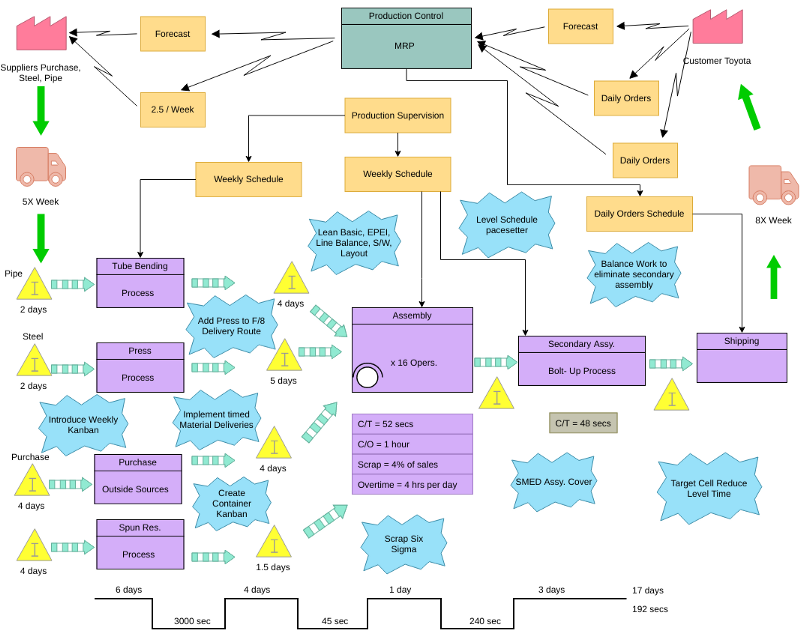
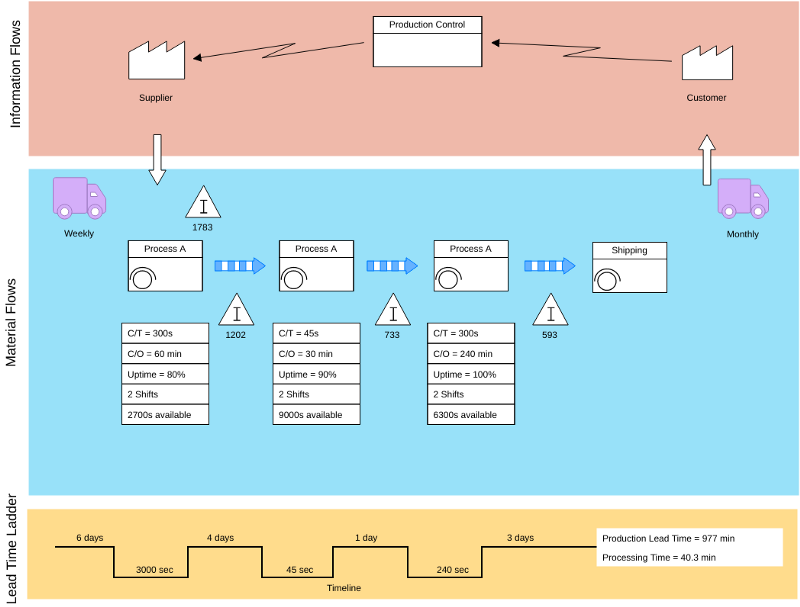
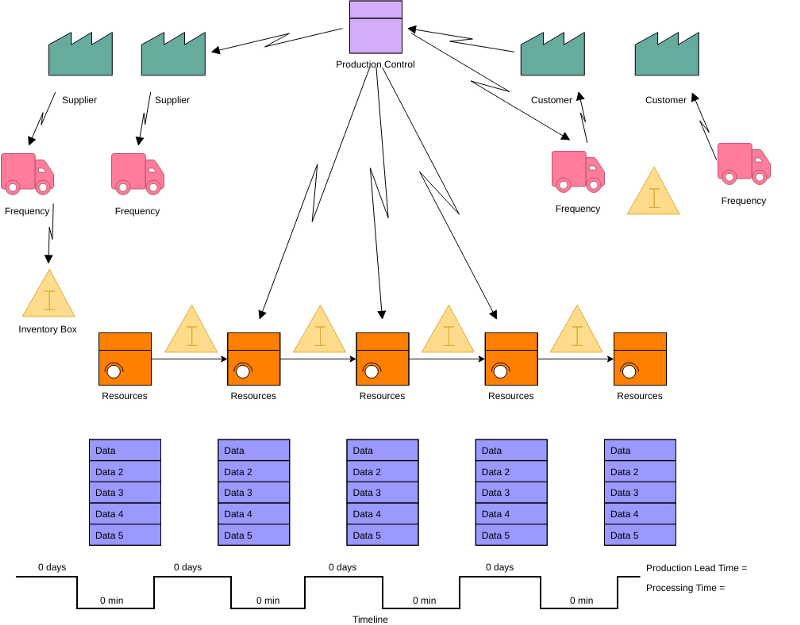
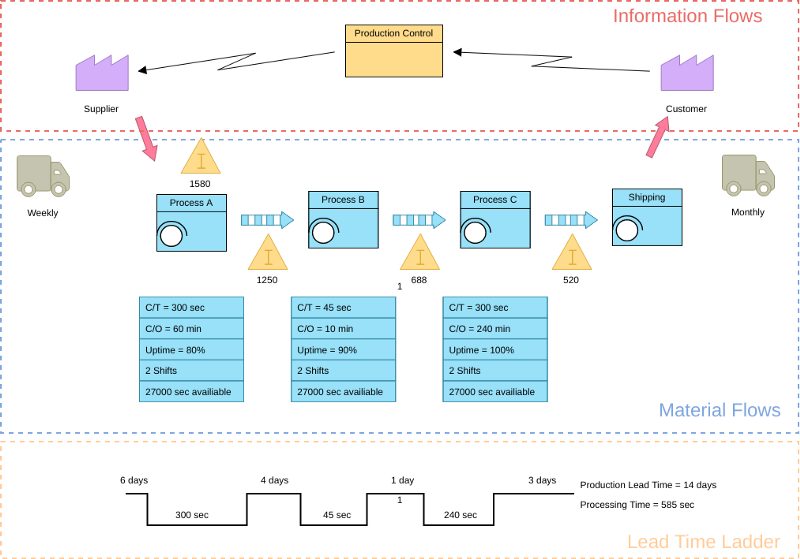
This post is also available in Deutsch, English, Español, فارسی, Français, Bahasa Indonesia, 日本語, Polski, Ру́сский, Việt Nam, 简体中文 and 繁體中文.